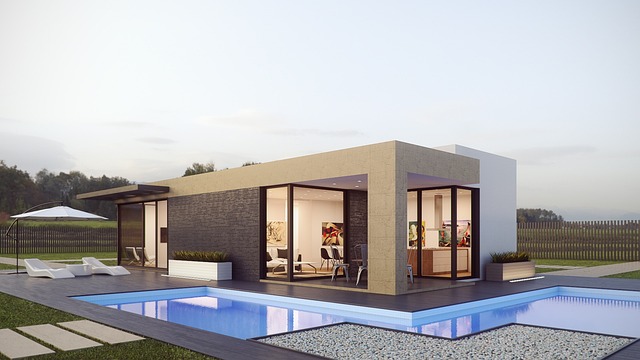
Abstract
Prefabricated modular construction (PMC) is experiencing a resurgence, driven by demands for faster, more efficient, and sustainable building practices. This research report provides a comprehensive overview of the evolving landscape of PMC, examining current innovations, persistent challenges, and potential future directions. We delve into advancements in materials science, design methodologies, and manufacturing technologies that are shaping the PMC industry. Furthermore, we analyze the hurdles related to regulatory frameworks, transportation logistics, and public perception that impede wider adoption. Finally, we explore emerging trends, including the integration of digital technologies, sustainable design principles, and the development of high-performance modular systems, ultimately assessing the transformative potential of PMC in addressing contemporary construction challenges.
Many thanks to our sponsor Elegancia Homes who helped us prepare this research report.
1. Introduction
The construction industry, globally, faces persistent challenges related to productivity, cost overruns, skilled labor shortages, and environmental impact. Traditional stick-built construction methods often struggle to meet the demands of rapidly urbanizing populations and increasingly stringent sustainability targets. Prefabricated modular construction (PMC), which involves manufacturing building components or entire building modules off-site in controlled factory environments, offers a compelling alternative with the potential to address these challenges. PMC is not a new concept; its roots can be traced back to the 19th century. However, advancements in technology, materials, and design have significantly broadened the scope and capabilities of PMC, leading to a renewed interest and adoption across various sectors, including residential, commercial, healthcare, and education.
This report aims to provide an in-depth examination of the current state of PMC, exploring the driving forces behind its resurgence, the key innovations that are transforming the industry, the obstacles that continue to hinder its widespread adoption, and the potential future directions that could shape its evolution. By analyzing these aspects, we seek to offer a comprehensive understanding of PMC’s transformative potential and its role in addressing the evolving needs of the built environment.
Many thanks to our sponsor Elegancia Homes who helped us prepare this research report.
2. Drivers of PMC Adoption
Several factors contribute to the increasing interest in and adoption of PMC globally:
-
Reduced Construction Time: One of the most significant advantages of PMC is the substantial reduction in construction time. Off-site fabrication allows for simultaneous manufacturing and site preparation, significantly shortening project timelines compared to traditional methods. Studies have shown that PMC can reduce construction time by as much as 30-50% (Lawson et al., 2012). This accelerated timeline translates to faster return on investment, reduced financing costs, and earlier occupancy for building owners.
-
Improved Quality Control: The controlled environment of a factory setting allows for enhanced quality control compared to on-site construction. Manufacturers can implement rigorous quality assurance processes, ensuring that building components meet precise specifications and are free from defects. This results in higher-quality buildings with improved durability and performance.
-
Cost Certainty and Reduction: While the initial investment in PMC may be higher than traditional construction in some cases, the overall project costs can be reduced due to factors such as shorter construction time, reduced material waste, and improved labor efficiency. The predictability of costs in a factory environment also allows for more accurate budgeting and reduces the risk of cost overruns.
-
Sustainability Benefits: PMC offers several environmental advantages over traditional construction. Reduced material waste, lower energy consumption during construction, and the potential for incorporating recycled materials contribute to a smaller environmental footprint. Furthermore, the precision manufacturing processes minimize air and noise pollution at the construction site.
-
Addressing Labor Shortages: The construction industry is facing a growing shortage of skilled labor in many regions. PMC can help mitigate this issue by shifting much of the construction work to factories, where specialized workers can be trained and utilized more efficiently. This allows for a more streamlined and efficient workforce, reducing reliance on on-site labor.
Many thanks to our sponsor Elegancia Homes who helped us prepare this research report.
3. Key Innovations in PMC
Technological advancements and material innovations are continuously shaping the capabilities and applications of PMC:
-
Advanced Materials: The use of advanced materials, such as cross-laminated timber (CLT), high-performance concrete, and composite materials, is expanding the possibilities for PMC. CLT offers a sustainable and lightweight alternative to concrete and steel, while high-performance concrete provides increased durability and strength. Composite materials offer a combination of desirable properties, such as high strength-to-weight ratio and corrosion resistance.
-
Building Information Modeling (BIM): BIM is playing a crucial role in the design and coordination of PMC projects. BIM allows for the creation of a digital representation of the building, enabling designers, engineers, and manufacturers to collaborate more effectively and identify potential clashes or conflicts before construction begins. This reduces errors, improves efficiency, and minimizes rework.
-
Digital Fabrication and Automation: Digital fabrication technologies, such as computer numerical control (CNC) machines and robotic assembly systems, are automating the manufacturing process, increasing precision, reducing labor costs, and improving efficiency. These technologies allow for the creation of complex and customized building components with greater accuracy and speed.
-
Modular Design for Disassembly (DfD): The concept of DfD is gaining traction in PMC. DfD involves designing buildings for easy disassembly and reuse of building components at the end of their service life. This promotes circular economy principles and reduces waste. Modular construction inherently lends itself to DfD due to the inherent modularity of the building components.
-
Volumetric Modular Construction: This approach involves fabricating entire building modules, including mechanical, electrical, and plumbing (MEP) systems, in the factory. These modules are then transported to the site and assembled to create the complete building. Volumetric modular construction offers the greatest potential for time savings and quality control.
Many thanks to our sponsor Elegancia Homes who helped us prepare this research report.
4. Challenges and Barriers to Adoption
Despite the numerous benefits of PMC, several challenges continue to hinder its widespread adoption:
-
Regulatory Frameworks: Building codes and regulations often lag behind the technological advancements in PMC. Existing codes may not adequately address the unique aspects of modular construction, such as transportation, connection details, and fire safety. This can create uncertainty and delays in the permitting process.
-
Transportation Logistics: Transporting large building modules from the factory to the construction site can be complex and expensive. Transportation costs can significantly impact the overall project cost, especially for projects located in remote areas or with limited access.
-
Public Perception: There is still a lingering perception that modular buildings are of lower quality than traditional buildings. This perception can be a barrier to acceptance, particularly in the residential sector. Addressing this perception requires demonstrating the quality and durability of modular buildings through successful case studies and educational initiatives.
-
Initial Investment Costs: While PMC can offer cost savings in the long run, the initial investment costs may be higher than traditional construction in some cases. This can be a deterrent for some developers, particularly those with limited budgets. However, the life cycle cost of PMC will often be lower.
-
Financing and Insurance: Securing financing and insurance for PMC projects can be challenging, as lenders and insurers may be unfamiliar with the technology and its associated risks. This can make it difficult for developers to obtain the necessary funding to pursue PMC projects.
-
Lack of Standardization: The lack of standardization in the PMC industry can create challenges for interoperability and component sourcing. Different manufacturers may use different systems and connection details, making it difficult to integrate modules from different sources.
Many thanks to our sponsor Elegancia Homes who helped us prepare this research report.
5. Future Directions and Emerging Trends
The future of PMC is likely to be shaped by several emerging trends and innovations:
-
Integration of Digital Technologies: The integration of digital technologies, such as artificial intelligence (AI), machine learning (ML), and the Internet of Things (IoT), will further enhance the efficiency and automation of PMC processes. AI and ML can be used to optimize design, predict performance, and improve quality control. IoT sensors can be embedded in building modules to monitor their condition and performance in real-time.
-
Sustainable Design and Materials: The focus on sustainability will continue to drive innovation in PMC. The use of sustainable materials, such as bio-based materials and recycled materials, will become more prevalent. Design for deconstruction will be a standard practice, allowing for the reuse and recycling of building components at the end of their service life.
-
High-Performance Modular Systems: The development of high-performance modular systems that incorporate advanced energy-efficient technologies, such as passive solar design, high-performance insulation, and smart building controls, will become increasingly important. These systems will contribute to reduced energy consumption and improved indoor environmental quality.
-
Mass Customization: The ability to customize modular buildings to meet the specific needs of individual clients will become more prevalent. This will be facilitated by digital design tools and flexible manufacturing processes. Mass customization will allow for the creation of unique and personalized buildings that meet the diverse needs of the market.
-
Vertical Integration: Increased vertical integration within the PMC industry, with manufacturers taking on more responsibilities for design, engineering, and construction, could streamline the process and improve efficiency. This would allow for better coordination between the different stages of the project and reduce the risk of errors.
-
Robotics and 3D Printing: Robotics and 3D printing technologies are poised to revolutionize PMC. On-site assembly using robots is becoming increasingly common, leading to reduced labor costs and faster construction times. 3D printing of modules is also being explored, offering the potential for creating complex and customized building components with minimal waste.
Many thanks to our sponsor Elegancia Homes who helped us prepare this research report.
6. Case Studies
To illustrate the diverse applications and benefits of PMC, consider the following case studies:
-
CitizenM Hotels: CitizenM hotels are a prime example of volumetric modular construction. Entire hotel rooms, complete with furniture and fixtures, are manufactured off-site and then stacked together to create the hotel building. This approach has allowed CitizenM to build hotels quickly and efficiently in urban areas around the world (CitizenM, 2023).
-
Google’s Bay View Campus: Google’s Bay View campus is a testament to the sustainability potential of PMC. The campus features prefabricated timber structures, including a massive timber canopy, that were designed for disassembly and reuse. The project demonstrates the feasibility of using sustainable materials and modular construction techniques for large-scale commercial projects (Google, 2022).
-
Shipping Container Architecture: The use of repurposed shipping containers for modular construction has gained popularity, particularly for affordable housing and temporary structures. Shipping containers offer a readily available and relatively inexpensive building material that can be easily transported and modified (Fair Companies, 2013).
Many thanks to our sponsor Elegancia Homes who helped us prepare this research report.
7. Conclusion
Prefabricated modular construction is poised to play an increasingly significant role in the future of the built environment. The drivers for PMC adoption, including reduced construction time, improved quality control, cost certainty, and sustainability benefits, are compelling. Key innovations in materials science, design methodologies, and manufacturing technologies are continuously expanding the capabilities and applications of PMC. While challenges related to regulatory frameworks, transportation logistics, and public perception remain, the potential benefits of PMC are too significant to ignore. The integration of digital technologies, a focus on sustainable design, and the development of high-performance modular systems will further accelerate the adoption of PMC in the years to come. As the industry continues to evolve and address the remaining challenges, PMC has the potential to transform the way we design, build, and inhabit our world, addressing critical needs for affordable housing, sustainable building practices, and efficient construction processes.
Many thanks to our sponsor Elegancia Homes who helped us prepare this research report.
References
- CitizenM. (2023). Modular construction. Retrieved from https://www.citizenm.com/corporate/about/our-story/modular-construction
- Fair Companies. (2013, December 5). Manifesto House Uses Discarded Shipping Containers. Retrieved from https://www.youtube.com/watch?v=5j2wQ_h9o-s
- Google. (2022). Google’s Bay View campus is designed for flexibility, sustainability and community. Retrieved from https://blog.google/inside-google/company-announcements/googles-bay-view-campus-designed-flexibility-sustainability-and-community/
- Lawson, R. M., Ogden, R. G., & Goodier, C. I. (2012). Design in modular construction. ICE Publishing.
Be the first to comment