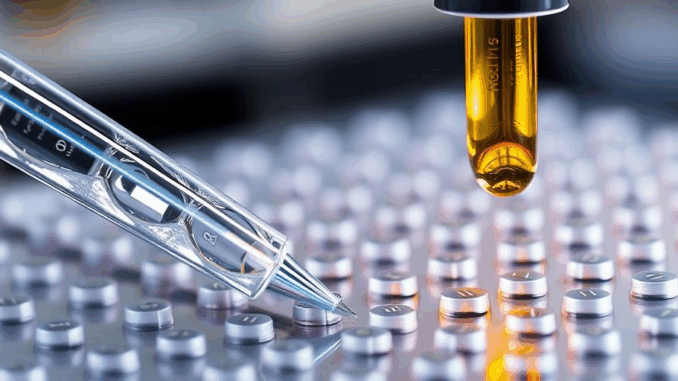
Advanced Functional Coatings: A Comprehensive Review of Materials, Deposition Techniques, Performance, and Future Trends
Abstract
Functional coatings represent a rapidly evolving field of materials science and engineering, offering tailored solutions to a diverse range of applications across industries such as construction, automotive, aerospace, biomedical, and electronics. This comprehensive review delves into the multifaceted aspects of advanced functional coatings, encompassing their material compositions, deposition techniques, performance characteristics, and emerging trends. We explore the fundamental principles governing the behavior of these coatings, focusing on key functionalities including corrosion resistance, wear resistance, optical properties (Low-E, Solar Control, and Self-Cleaning), thermal management, antimicrobial activity, and self-healing capabilities. We critically evaluate various deposition methods, such as physical vapor deposition (PVD), chemical vapor deposition (CVD), sol-gel processes, and electrochemical deposition, considering their advantages, limitations, and suitability for specific applications. Furthermore, this report examines the performance metrics used to assess the effectiveness of functional coatings, including adhesion, hardness, durability, and environmental stability. Finally, we discuss the latest advancements and future directions in the field, highlighting the potential of nanotechnology, bio-inspired coatings, and smart materials to revolutionize the functionality and performance of coatings for next-generation applications.
1. Introduction
Coatings, in their simplest form, serve as protective barriers against environmental degradation. However, the realm of functional coatings extends far beyond mere protection. These advanced materials are engineered to impart specific properties and functionalities to surfaces, enabling enhanced performance, extended lifespan, and novel capabilities. The demand for functional coatings is driven by the ever-increasing need for materials with improved durability, energy efficiency, sustainability, and specialized performance in demanding environments. This report provides a comprehensive overview of the science and technology behind functional coatings, encompassing their diverse material compositions, deposition techniques, performance metrics, and emerging trends. The scope is deliberately broad to capture the interdisciplinary nature of the field and to provide a holistic perspective for experts working in specific areas of coating technology. The coatings are intended to have different functions, and as such, the material selection and manufacturing process is very important.
2. Material Compositions for Functional Coatings
The selection of appropriate materials is paramount to achieving the desired functionality in a coating. The vast array of materials employed in functional coatings can be broadly categorized as follows:
-
2.1. Inorganic Coatings: Inorganic coatings are characterized by their high thermal stability, hardness, and resistance to degradation. They are commonly used for applications requiring high durability and protection in harsh environments. Common types include:
- 2.1.1. Ceramic Coatings: These coatings, composed of metal oxides, carbides, nitrides, or borides, offer excellent wear resistance, corrosion resistance, and thermal barrier properties. Examples include alumina (Al2O3), titania (TiO2), zirconia (ZrO2), and silicon carbide (SiC). The performance of ceramic coatings can be further tailored by doping or incorporating multiple phases to achieve specific properties.
- 2.1.2. Metallic Coatings: Metallic coatings, such as chromium, nickel, titanium, and aluminum, are widely used for corrosion protection, wear resistance, and aesthetic appeal. These coatings can be applied through various techniques, including electroplating, electroless plating, and thermal spraying. The performance of metallic coatings is strongly influenced by the grain size, crystallographic orientation, and presence of defects.
- 2.1.3. Glass Coatings: Glass coatings, often applied as thin films, provide excellent optical properties, chemical resistance, and electrical insulation. They are commonly used in architectural glazing for energy-efficient windows and solar panels. The composition of the glass can be tailored to achieve specific refractive indices, transmittance, and reflectance.
-
2.2. Organic Coatings: Organic coatings, based on polymers and resins, offer versatility, flexibility, and ease of application. They are widely used for decorative purposes, corrosion protection, and as functional layers in various applications. Key types include:
- 2.2.1. Polymer Coatings: Polymer coatings, such as acrylics, epoxies, polyurethanes, and silicones, provide a wide range of properties, including flexibility, chemical resistance, and weatherability. The choice of polymer depends on the specific application requirements and desired performance characteristics. The use of polymers is increasing due to their versatility.
- 2.2.2. Composite Coatings: Composite coatings combine organic and inorganic materials to achieve synergistic properties. For example, incorporating nanoparticles into a polymer matrix can enhance the mechanical strength, scratch resistance, and barrier properties of the coating. Common nanoparticles used in composite coatings include silica, alumina, and carbon nanotubes.
-
2.3. Hybrid Coatings: Hybrid coatings bridge the gap between inorganic and organic materials, offering a combination of their respective advantages. These coatings typically consist of an inorganic network modified with organic functionalities, allowing for tailored properties such as flexibility, hardness, and chemical resistance. Sol-gel processes are commonly used to synthesize hybrid coatings.
-
2.4. Emerging Materials: The field of functional coatings is constantly evolving with the development of new materials and concepts. Some emerging materials include:
- 2.4.1. Graphene and Other 2D Materials: Graphene and other two-dimensional materials, such as molybdenum disulfide (MoS2) and hexagonal boron nitride (hBN), exhibit exceptional mechanical, electrical, and thermal properties, making them promising candidates for advanced functional coatings. They can be used to enhance the strength, conductivity, and barrier properties of coatings.
- 2.4.2. Self-Healing Polymers: Self-healing polymers contain embedded healing agents that are released upon damage, allowing the coating to autonomously repair itself. These coatings offer enhanced durability and extended lifespan in demanding applications.
- 2.4.3. Bio-Inspired Materials: Bio-inspired materials mimic the structures and functionalities found in nature to create advanced coatings with unique properties. For example, lotus leaf-inspired coatings exhibit superhydrophobic properties, while gecko-inspired coatings provide strong adhesion.
3. Deposition Techniques for Functional Coatings
The deposition technique plays a critical role in determining the microstructure, properties, and performance of functional coatings. A wide variety of deposition methods are available, each with its own advantages and limitations. Key techniques include:
-
3.1. Physical Vapor Deposition (PVD): PVD techniques involve the vaporization of a source material and its subsequent condensation onto a substrate in a vacuum environment. Common PVD methods include:
- 3.1.1. Sputtering: Sputtering involves bombarding a target material with energetic ions, causing atoms to be ejected and deposited onto the substrate. Sputtering is a versatile technique that can be used to deposit a wide range of materials, including metals, ceramics, and polymers.
- 3.1.2. Evaporation: Evaporation involves heating a source material in a vacuum environment until it vaporizes and condenses onto the substrate. Evaporation is a relatively simple technique that is well-suited for depositing metals and some inorganic compounds.
- 3.1.3. Pulsed Laser Deposition (PLD): PLD involves using a pulsed laser beam to ablate material from a target and deposit it onto the substrate. PLD is a versatile technique that can be used to deposit complex materials with precise stoichiometry.
-
3.2. Chemical Vapor Deposition (CVD): CVD techniques involve the reaction of gaseous precursors on a heated substrate to form a solid coating. CVD offers excellent conformality and control over the coating composition. Common CVD methods include:
- 3.2.1. Thermal CVD: Thermal CVD involves using thermal energy to drive the chemical reactions between the precursors.
- 3.2.2. Plasma-Enhanced CVD (PECVD): PECVD uses a plasma to enhance the chemical reactions, allowing for lower deposition temperatures and improved coating properties.
- 3.2.3. Atomic Layer Deposition (ALD): ALD involves the sequential exposure of the substrate to different precursors, resulting in the layer-by-layer growth of the coating with atomic-level control.
-
3.3. Sol-Gel Processing: Sol-gel processing involves the synthesis of a colloidal solution (sol) that is then transformed into a solid gel network. The gel can be deposited as a coating by dipping, spraying, or spin-coating. Sol-gel processing offers a cost-effective and versatile route to producing a wide range of coatings, including ceramics, glasses, and hybrid materials.
-
3.4. Electrochemical Deposition: Electrochemical deposition involves the reduction or oxidation of ions in an electrolyte solution onto an electrode surface, resulting in the formation of a solid coating. Electrochemical deposition is widely used for depositing metals and alloys, and it offers excellent control over the coating thickness and composition.
-
3.5. Thermal Spraying: Thermal spraying involves melting or softening a coating material and propelling it onto a substrate, where it solidifies and forms a coating. Thermal spraying is a versatile technique that can be used to deposit a wide range of materials, including metals, ceramics, and polymers. Common thermal spraying methods include:
- 3.5.1. Plasma Spraying: Plasma spraying uses a plasma torch to heat and propel the coating material.
- 3.5.2. High-Velocity Oxy-Fuel (HVOF) Spraying: HVOF spraying uses a combustion flame to heat and propel the coating material at high velocities.
- 3.5.3. Cold Spraying: Cold spraying involves propelling solid particles of the coating material onto the substrate at high velocities, causing them to deform and bond to the surface without melting. Cold spraying offers the advantage of minimizing oxidation and phase transformations during the deposition process.
The selection of the appropriate deposition technique depends on the specific coating material, substrate, and desired performance characteristics. Each technique has its own advantages and limitations in terms of cost, deposition rate, coating quality, and applicability to different materials. For example, ALD offers exceptional conformality and thickness control, but it is a relatively slow and expensive process. Thermal spraying, on the other hand, is a cost-effective and high-throughput technique, but it may result in coatings with higher porosity and lower adhesion.
4. Performance Metrics for Functional Coatings
The performance of functional coatings is assessed based on a variety of metrics that reflect their ability to meet specific application requirements. Key performance metrics include:
-
4.1. Adhesion: Adhesion is the strength of the bond between the coating and the substrate. Good adhesion is essential for preventing delamination and ensuring the long-term durability of the coating. Adhesion is typically measured using pull-off tests, scratch tests, or indentation tests.
-
4.2. Hardness: Hardness is the resistance of the coating to indentation or scratching. High hardness is desirable for applications requiring wear resistance and scratch resistance. Hardness is typically measured using Vickers or Knoop microhardness testers.
-
4.3. Wear Resistance: Wear resistance is the ability of the coating to withstand abrasive or erosive wear. Wear resistance is typically measured using pin-on-disk tests, abrasive wear tests, or erosion tests.
-
4.4. Corrosion Resistance: Corrosion resistance is the ability of the coating to protect the substrate from corrosion in aggressive environments. Corrosion resistance is typically measured using electrochemical techniques, such as potentiodynamic polarization and electrochemical impedance spectroscopy (EIS), or by exposing the coated samples to corrosive environments and monitoring the rate of corrosion.
-
4.5. Optical Properties: Optical properties, such as transmittance, reflectance, and absorption, are important for coatings used in optical applications, such as solar control coatings and anti-reflective coatings. Optical properties are typically measured using spectrophotometry or ellipsometry.
-
4.6. Thermal Properties: Thermal properties, such as thermal conductivity and thermal expansion coefficient, are important for coatings used in thermal management applications, such as thermal barrier coatings. Thermal properties are typically measured using laser flash analysis or differential scanning calorimetry (DSC).
-
4.7. Environmental Stability: Environmental stability is the ability of the coating to maintain its properties and performance over time when exposed to various environmental factors, such as temperature, humidity, UV radiation, and chemical exposure. Environmental stability is typically assessed by exposing the coated samples to accelerated aging tests and monitoring the changes in their properties.
-
4.8. Functional Performance: This refers to the specific performance characteristic the coating is designed to deliver. Examples include:
- 4.8.1. U-value (Thermal Transmittance): Primarily relevant to Low-E coatings. Lower U-values indicate better insulation, reducing heat transfer through the glazing.
- 4.8.2. Solar Heat Gain Coefficient (SHGC): Critical for solar control coatings. A lower SHGC means less solar heat enters a building, decreasing cooling costs.
- 4.8.3. Visible Transmittance (VT): Measures the amount of visible light that passes through the coating. It impacts the natural lighting inside a building.
- 4.8.4. Contact Angle: For self-cleaning coatings, a high contact angle is desired, indicating superhydrophobicity. Water droplets bead up and roll off, carrying away dirt and debris. The smaller the contact angle the less hydrophobic it is.
The relative importance of each performance metric depends on the specific application requirements. For example, adhesion and corrosion resistance are critical for protective coatings used in harsh environments, while optical properties are paramount for coatings used in optical devices.
5. Emerging Coating Technologies and Future Trends
The field of functional coatings is continuously evolving, driven by the demand for enhanced performance, sustainability, and novel functionalities. Several emerging technologies and future trends are shaping the landscape of functional coatings:
-
5.1. Nanotechnology-Enabled Coatings: Nanotechnology offers unprecedented opportunities to tailor the properties of coatings at the nanoscale. Incorporating nanoparticles, nanowires, or nanotubes into coatings can enhance their mechanical strength, scratch resistance, barrier properties, optical properties, and electrical conductivity. For example, incorporating TiO2 nanoparticles into coatings can impart photocatalytic self-cleaning properties, while adding carbon nanotubes can enhance the electrical conductivity and mechanical strength.
-
5.2. Bio-Inspired Coatings: Bio-inspired coatings mimic the structures and functionalities found in nature to create advanced materials with unique properties. For example, lotus leaf-inspired coatings exhibit superhydrophobic properties due to their hierarchical surface structure, while gecko-inspired coatings provide strong adhesion due to their van der Waals interactions. These bio-inspired coatings are very innovative.
-
5.3. Self-Healing Coatings: Self-healing coatings contain embedded healing agents that are released upon damage, allowing the coating to autonomously repair itself. These coatings offer enhanced durability and extended lifespan in demanding applications. Self-healing can be achieved through various mechanisms, such as encapsulation of healing agents, reversible bond formation, or shape memory effects.
-
5.4. Smart Coatings: Smart coatings are designed to respond to changes in their environment, such as temperature, pressure, pH, or light. These coatings can change their properties or functionalities in response to these stimuli, enabling a wide range of applications, such as sensors, actuators, and adaptive camouflage.
-
5.5. Environmentally Friendly Coatings: The development of environmentally friendly coatings is driven by increasing environmental regulations and consumer demand for sustainable products. These coatings utilize renewable resources, reduce volatile organic compound (VOC) emissions, and minimize the use of hazardous materials. Examples include waterborne coatings, powder coatings, and bio-based coatings.
-
5.6. Additive Manufacturing of Coatings: Additive manufacturing, also known as 3D printing, is emerging as a promising technique for fabricating coatings with complex geometries and tailored properties. Additive manufacturing techniques, such as laser cladding, direct energy deposition, and inkjet printing, can be used to deposit coatings with high precision and control over the microstructure and composition.
The future of functional coatings is expected to be driven by the integration of these emerging technologies and the development of multifunctional coatings that can address multiple performance requirements simultaneously. These advanced coatings will play a crucial role in enhancing the performance, durability, and sustainability of materials and products across a wide range of industries.
6. Conclusion
Functional coatings have emerged as a critical enabling technology for a wide range of applications, offering tailored solutions to enhance the performance, durability, and functionality of surfaces. This comprehensive review has explored the diverse materials, deposition techniques, performance metrics, and emerging trends in the field of functional coatings. The selection of appropriate materials and deposition techniques is crucial for achieving the desired performance characteristics, while emerging technologies such as nanotechnology, bio-inspired materials, and self-healing concepts are paving the way for advanced coatings with unprecedented capabilities. As the demand for high-performance and sustainable materials continues to grow, functional coatings will play an increasingly important role in shaping the future of materials science and engineering. Further research and development efforts are needed to overcome the challenges associated with cost, scalability, and long-term durability, enabling the widespread adoption of these advanced coatings in various industries.
References
- ASM Handbook, Volume 5A: Thermal Spray Technology
- Handbook of Thin Film Technology
- Coatings Technology Handbook
- Nanomaterials in Coatings
- Surface Engineering for Corrosion and Wear Resistance
- Low-E Glass: Everything You Need to Know
- Solar Control Window Film: A Guide to Energy Savings
- Self-cleaning coatings.
So, if we make coatings that mimic gecko feet AND lotus leaves, will my car be able to drive upside down and clean itself simultaneously? Asking for a friend… who is me.
Self-healing polymers, eh? So, if my coated car gets a scratch, it’ll just…fix itself? Does this mean I can finally stop pretending to know how to use touch-up paint, or will I still need to worry about bird droppings etching the finish?
The review highlights the exciting potential of bio-inspired coatings, particularly those mimicking the lotus leaf for superhydrophobicity. How might these self-cleaning properties be optimized for large-scale applications, such as building exteriors, considering cost-effectiveness and durability against environmental pollutants?
So, we’re basically talking about giving materials superpowers, huh? Forget repainting; maybe we’ll just 3D print entire buildings with coatings that adjust to the weather like some kind of futuristic mood ring. I’m picturing skyscrapers changing color with the seasons!
So, coatings are getting smarter? Forget about choosing a paint color; will we soon be arguing about which “smart coating personality” best suits our living room? I’m picturing coatings that change color based on my mood lighting.
The discussion on deposition techniques is quite comprehensive. Considering the increasing focus on sustainability, how do techniques like cold spraying or ALD compare in terms of energy consumption and waste generation, and what innovations are being pursued to further minimize their environmental footprint?
This review comprehensively highlights the advancements in deposition techniques. How might we adapt these methods to create coatings with dynamically tunable properties, responding in real-time to environmental changes or user input, thereby expanding their application in adaptive optics or smart textiles?
This review comprehensively covers deposition techniques. What are the challenges in scaling up ALD for large surface areas while maintaining uniformity and cost-effectiveness, especially for applications like flexible electronics or large architectural panels?
Considering the rise of additive manufacturing, how might we tailor the composition of coatings during the printing process to achieve spatially varying properties within a single coating layer, optimizing performance in specific areas?
Given the rise of bio-inspired and self-healing coatings, how might we integrate these functionalities to create coatings that not only mimic natural properties but also autonomously repair damage, extending the lifespan and performance of coated materials?